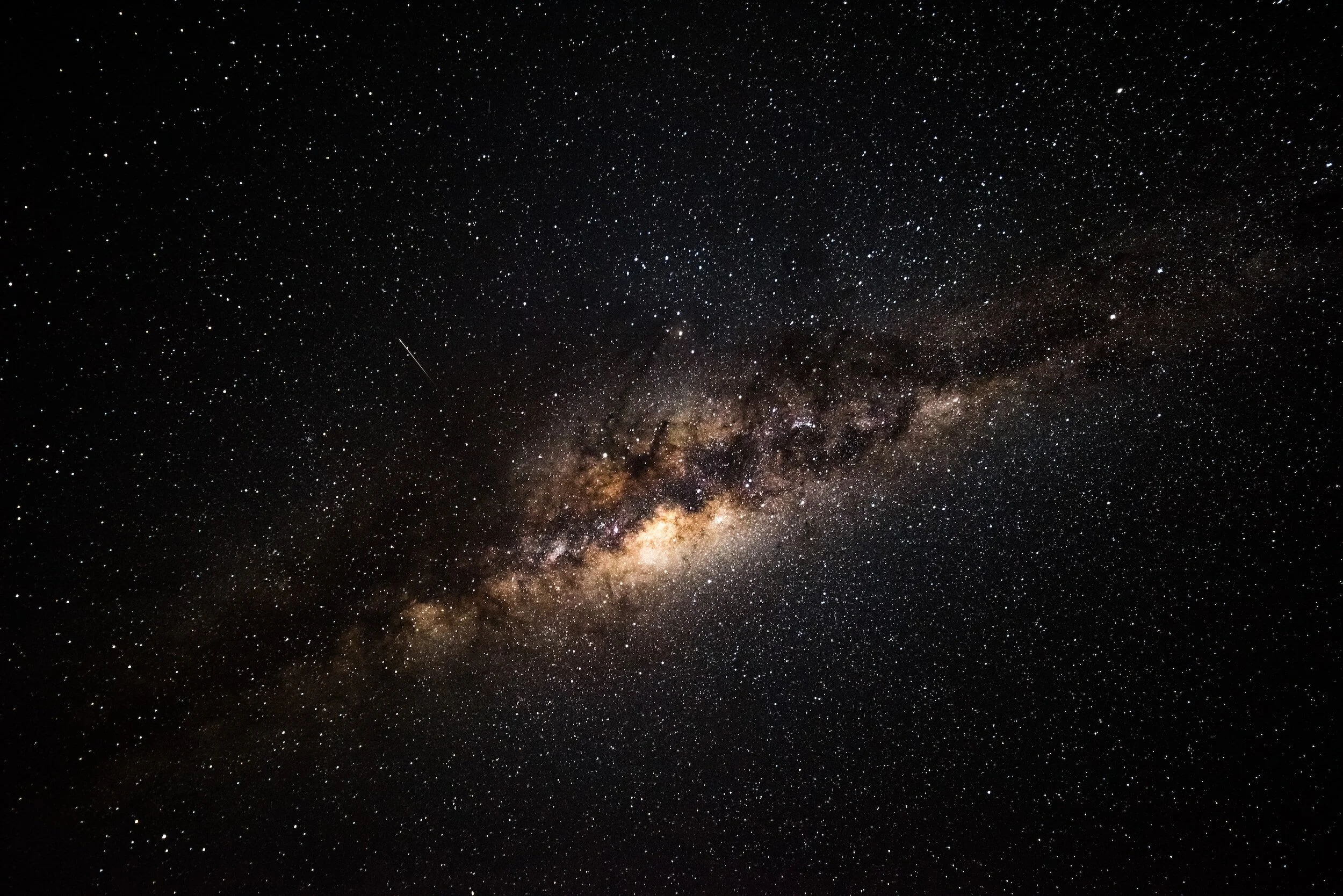
Projects
Project Pegasus (Rutherford-type Rocket, NOX and Ethanol Propellants)
Photo Taken in December 2024
Situation: Senior Capstone for me and my close friend to build this 5kN Rocket to submit to AIAA Conference Research Paper on Rutherford Types Rocket Engine inspired by Rocket Lab
Task: Design hydraulic schematic of rocket engine, rocket nozzles, injectors, and isentropic and cooling parameters of the rocket
Action:
Start reading books and researches, scouting available designs, and potential dangers regarding of Compressible Flow, Injector, Nanodroplets, Combustion Instability, and Isentropic Relations
Built a Simulink model to simulate Rocket Engine Thrust Curve, OF Ratio, Fluid Velocity, and Pressure. Then, performing a 3D Simulation on Ansys to re-verify the SolidWorks CAD designs
Create a 3D-printed model to conduct cold-water testing and verify assembly feasibility. Then, send out for shop to machine the actual components with GD&T verified.
Result: Ongoing, wait until Spring 2025
What I Learned: I’m exposed into various technical areas, including thermal analysis, fluid systems, combustion, cooling and nanodroplet behavior, compressible and incompressible flow, and Fluid Simulink for hydraulic schematic. This project by far is the most technical project I’ve ever done.
Hydraulic System on Simulink I designed to simulate real-time Thrust Curve
Hydraulic Schematic Drafting:
Mars Rover BILL-EE (1st Rover of Cal Poly Pomona)
Situation: Tasked with directing a Mars rover project for the University Rover Challenge (URC) 2024, leading a team of 20 STEM students.
Task: My responsibilities included managing the team, designing essential components, and ensuring the rover met specific mission requirements according to URC guidelines & requirements
Action:
Management: Guided and coordinated the team's efforts in various aspects of the project.
Technical Work: Calculated and design dynamic and structural integrity of the rovers to ensure its capability to qualify for URC’s mission
Collaboration: Worked closely with other STEM students to develop testing and integration plans, ensuring the rover met the 50kg payload requirement and URC's mission criteria.
Result: Successfully led the Cal Poly Pomona Rover team to pass the System Acceptance Review (SAR) phase of the University Rover Challenge (URC) 2024 for the first time and become a URC 2024 Finalists
What I Learned: Project BILL-EE marked my first experience in managing a large student team for an international competition. Through this project, I gained valuable insights into directing collaboration among team members, developing technical plans for system testing, and enhancing my leadership and financial management skills. Besides management responsibilities, I also exposed into various technical areas, including thermal analysis, fluid systems, dynamic systems, programming languages, and robotic simulation. Although I’m stepping down from the leader of the team, this will be always my most remarkable memory I’ll ever have.
5-Axis Robotic Arm
Made in Fall 2023
Situation: Create a 5-axis robotic arm, ensuring functionality in extreme conditions.
Task: My goal is to design a lightweight robotic arm under a 6kg system, having the capability of lifting 5kg and reaching 1.4m, suitable for operation in high-temperature environments. The budget is under $1500, motor voltage must be at 12-24V range
Action:
I chose to design and manufacture with Aluminum 6061-T6 and ASA filament for minimal weight, maximum rigidity, thermal resistance, and compatible with the limited budget
Calculate the torque, speed requirements at each axis of the Robotic Arm to properly size the appropriate motor for the applications
Developed a MATLAB program to simulate the inverse kinematics behavior of the robotic arm.
Result: I successfully designed a robotic arm weighing 5.2kg, with a maximum reach of up to 1.4m, able to lift up to 6kg. The total cost for the project was $900, and all parts of the structure are capable of operating at temperatures of 110°F, a standard Utah environment.
What I Learned:
This project is the first time I have been introduced to advanced MATLAB/Simulink, Python, C++ programming to control a robotic system. I learned how to implement inverse kinematic calculations to acquire changes in forward dynamics. Also, I am currently learning how to integrate collision detection into the arm to estimate any contact points that may occur between the arm and the rover.
Robotic Arm Lift 15 lb. Weight
2D Simulation of Robotic Arm Inverse Kinematic with Embedded PID based on Encoder Feedback
Robotic Arm Inverse Kinematic with PID Calibration to balancing a bolt on it
Industrial 0.75 HP - 30,000 RPM Planetary Gearbox
Situation: Design for Machine Design class for an industrial 0.75 HP, 30000 RPM speed and last for 20,000 hours. A NASA will review the final product contractor and employee
Task: My responsibilities included designing a CAD model, calculating the failure modes of the gearbox to ensure it can operate properly and last 20,000 hours
Action:
I examined the parameters carefully and evaluated what I should value and
I started digging into multiple research, reading about advanced gear design such as AGMA and JIS.
Using the available data, I start designing the gearbox and select the appropriate motor based on the parameters calculated
Result: The final result is the gearbox able to run up to 40,000 RPM, last 25,000 hours, and only cost $550. The cheapest design in the class for industrial standards.
What I Learned:
I learned significantly a lot of information regarding industrial motor design and high-speed rotary systems, especially restraints with the 20,000+ operating hours. This project is the first time I get to introduce with concept of tolerance stack up, GD&T requirements in industrial design
Started in Summer 2024
Martian Cave Rover Caveman
Made in Spring 2022
Situation: Tasked with designing the 'Caveman' rover for NASA's L' Space Martian cave exploration, focusing on complex robotic dynamics and extreme environmental analysis.
Task: Develop a rover capable of operating in Mars's extreme cave conditions, withstanding Mars temperatures up -80°F, radiation, and having the capabilities to measure temperature, humidity, and radiation.
Action:
I chose a four-legged robotic system equipped with 3-axis per leg to ensure the rover able to overcome a variety of Martian cave condition
For withstanding temperatures as low as -80°F and extreme radiation, I chose Ti-6Al-4V as the main structure material for its excellent thermal coefficients, with layers of Aerogel for maximizing temperature insulation, a Kapton heater, and a radiator for overheating situations.
With measuring radiation, temperature, and humidity, we have decided to stay with the ACRE system for measuring environmental data as it has been proven to be effective and reliable on the Perseverance rover
Result: We accomplished a 165-page PDR, and being highly appraised by NASA engineers behind the technical aspect of the project and the detail it provides.
What I Learned:
I was a sophomore at the time, and this project was the first opportunity I had to be exposed to a large-scale project and a significant program like NASA's L' Space MCA. I learned a great deal about advanced SolidWorks features and CAD skills for controlling large assemblies. Furthermore, this project is the first time I put my hand on FEM Analysis before taking any classes related to this subject
Bio-Weapon Detector Cyclone
(On Progress)
Situation: Engaged in a project to advance bio-detection technology, focusing on the design of a cyclone separator for identifying five distinct bio-organisms.
Task: The aim was to develop a cyclone separator that uses air and PBS buffer to separate bio-organisms from the air, transport the solution to the immunoassay, and analyze it with a sensor system for real-time reporting.
Action:
I designed the cyclone separator based on C.J. Stairmand and used an Arctic 40x40x28 axial fan to ensure its efficiency in separating and being able to deliver 12.06 m³/h of air
Working on C++ programming on a Raspberry Pi 4B to integrate immunoassay data with a five-sensor system, enabling accurate and immediate data reporting.
Successfully presented the project’s potential, securing a significant $8,000 funding grant from the U.S. National Science Foundation (NSF).
Result: Successfully presented the project’s potential, securing a significant $8,000 funding grant from the U.S. National Science Foundation (NSF).
What I Learned:
Project CYCLONE was my first experience with fluid simulation and calculations. This project taught me about integrating different areas of the STEM field, including the Science, Electrical, Software, and Mechanical aspects
Made in Spring 2023
Stair Climbing Vehicle
Made in Spring 2023
Situation: Project assignment for ME2331 class
Task: Design a stair climbing vehicle on a 30-degree incline, under a $100 budget, maximum of 8x AA batteries, and must climb up within 6 minutes and go down within 3 minutes with a minimal amount of water spill
Action: I used 4x 12V worm gears to ensure enough torque to drive the vehicles, with a gimbal for holding the water cup, and silicone tape wheels for maximum traction
Result: The vehicle successfully climbed up the stairs within 3 minutes and 30 seconds, while climbing down within 1 minute and 40 seconds. The amount of spilled water is only 20% while climbing down.
What I Learned:
I developed this project in my ME2331 class at the beginning of my junior year. The primary challenge was to design a mechanism capable of climbing a stair with a roughly 20-degree incline within a specific timeframe. This project taught me how to collaborate effectively with classmates and evaluate all the constraints required to deliver the best possible technology within a set budget and mission parameters.
Other Projects
Artemis Red Habitable Mobility Platform
Made in Winter 2021
Chevrolet Camaro
Made in Summer 2021
Sunkist Orange Juicer
Made in Fall 2020
NASA SUITS Proposal
Made in Winter 2021
NCAS Phase I HOPER Project
Made in Spring 2021