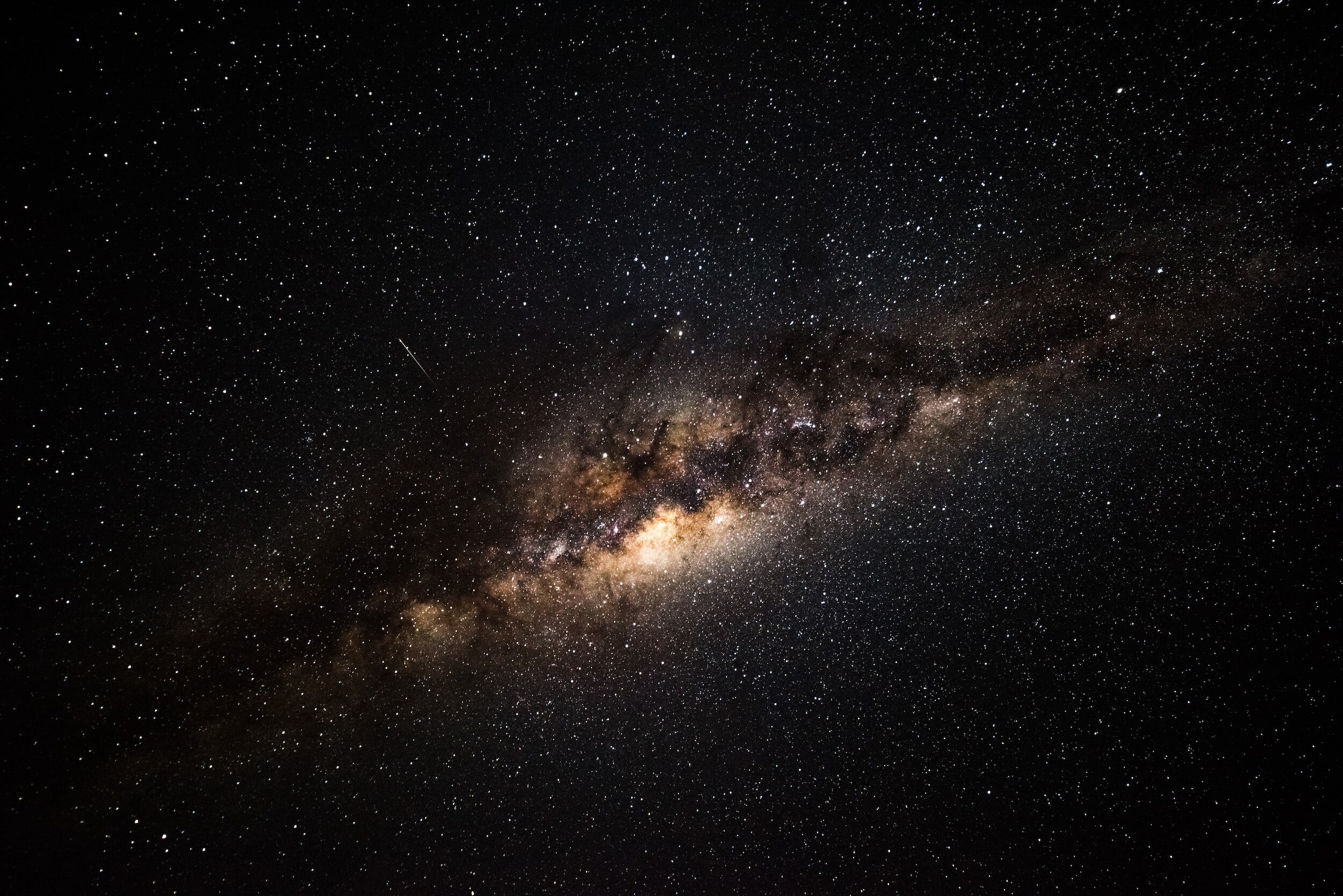
Internship
Notice: The images displayed on this site are used exclusively for visualization. I am committed to upholding intellectual property rights, ensuring these images do not expose any proprietary information.
Automation of CATIA V5 Surfacing
Problem: Surfacing a “specific feature” at Tesla causing a huge delay in project progress and increasing workloads on the engineers
Solution: By studying the topological world of curvatures, string objects, and addressing randomness challenges, I developed a mathematical approach to compute an inconsistent CATIA V5 surfacing at Tesla. Using only 2x user inputs, this method achieved an accuracy of 80-90%.
Testing: Tests were conducted on 10 Tesla Semi surfacing parts, with time metrics recorded during program usage to evaluate performance and efficiency.
Result: The programs successfully reduced the surfacing process time by 30-50%, resulting in an overall stamping surfacing project time reduction of 5-10% per Tesla stamping part.
Tesla Semi Surfacing Projects
Problem: Tasked with designing a die surfacing cavity for Tesla Semi parts to ensure smooth metal transitions with minimal thinning and wrinkling.
Solution: Collaborated with a mentor to study and implement innovative surfacing design patterns, implementing engineering analysis of metal stamping flow through AutoForm to optimize structures manufacturability.
Result: Successfully reduce thinning on stamping parts from 32% to 14%, surfaces are accepted into production
Notice: The images displayed on this site are used exclusively for visualization. I am committed to upholding intellectual property rights, ensuring these images do not expose any proprietary information.
Machine-Learning Forging Load Prediction
Problem: High frequency of wrong estimation on initial forging load causing engineers and technicians to go through multiple trials
Solution: I implemented the Slab Analysis Method into a MATLAB code to estimate the initial forging load required for Closed-Die Forging, prior to using DEFORM Simulation. Afterward, I built a machine-learning program to compute the previous data to predict correct future forging loads
Testing: To verify the calculation, I used Digital Wavelength Infrared Pyrometry to ensure the temperature was accurate and aligned with the Strength Coefficient of aluminum under the specified conditions. After that, I carefully and correctly coated the surface of the metal to allow the smooth flow of plastic metal. Then, I compared the testing load derived from the calculation with the previously proven correct testing load for validation.
Results: Prediction reach 85% accurate for future forging load
Metal 3D-Print CNC Insert Holder
Problem: The large Titanium/Inconel CNC machine often crashes its tools into the part or fixtures, damaging the metal holder and incurring a replacement cost of roughly $500-750.
Solution: A junior engineer at PCC came up with the idea of using Metal 3D Printing for the CNC machine and asked me to assist with the analysis, printing process, and performance evaluation of the holder.
My Assist: Based on my calculations, using 3D-printed metal for this application is cost-effective, as it only costs approximately $10-40 per piece (including sintering), compared to the purchasing cost of $500-750 for traditional parts. With a budget of under $8,000, I selected the Ultimaker S7, while using PVA (soluble filament) for large draft structures. This approach improves surface finish, prevents warping, and reduces time spent on support removal. For the metal filament, we chose BASF Ultrafuse 316L Metal (Stainless Steel). To accommodate for size reduction during sintering, all parts in the z-axis dimension were designed slightly larger.